At the end of last year, planned investments in technologies for expanding the production of next generation tapered and axle bearings were completed at the ZKL plant in Brno. Production has been in full operation since the beginning of the year.
New production machines and fully automated quality control devices for bearings for railway and other industrial applications have been installed and put into operation in the newly reconstructed halls.
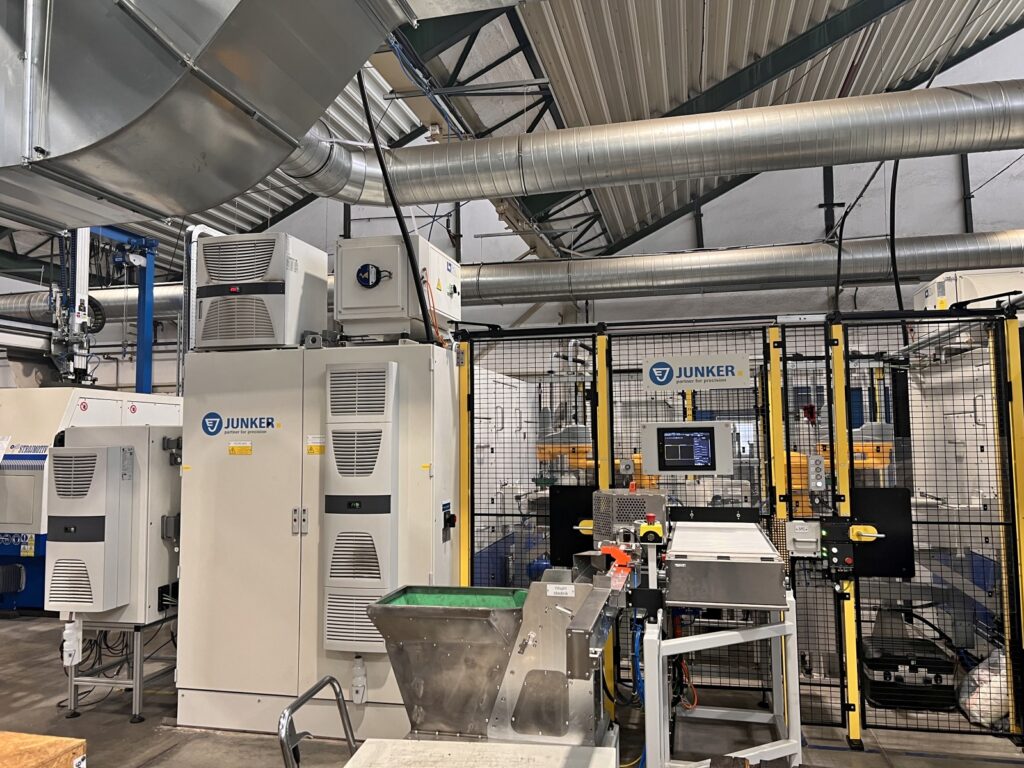
Just like in other industries, reliability of individual parts is highly emphasized in the railway industry as well. “We are aware that the quality of bearings does not depend solely on the quality of the rings,” says ZKL Group’s Technical Director Libor Nohál. “Therefore, we have also acquired a robotic cell for grinding rolling elements for our new machine park. The quality of roller and tapered surfaces, the presence of defects such as cracks, burns, and the like, is therefore checked in a robotic workplace on automated equipment using eddy currents,” he adds.
Eddy current testing is a non-destructive testing (NDT) method used for various purposes, including defect detection, measuring material and coating thickness, identifying material, and determining the condition of heat treatment of certain materials. The significance of investments is also commented on by ZKL’s CEO Jiří Prášil Jr.: “We are a traditional Czech manufacturer of bearings not only for the railway industry. In the last 3 years, we have multiplied the volume of production and sales of bearings, especially for railway applications, so we have invested in expanding production in both manufacturing plants in Brno and Klášterec nad Ohří.” He further mentions, “These steps lead to the fulfilment of our strategy, providing customers with a comprehensive range of premium quality railway bearings and comprehensive solutions for more reliable and safer mobility tomorrow.”